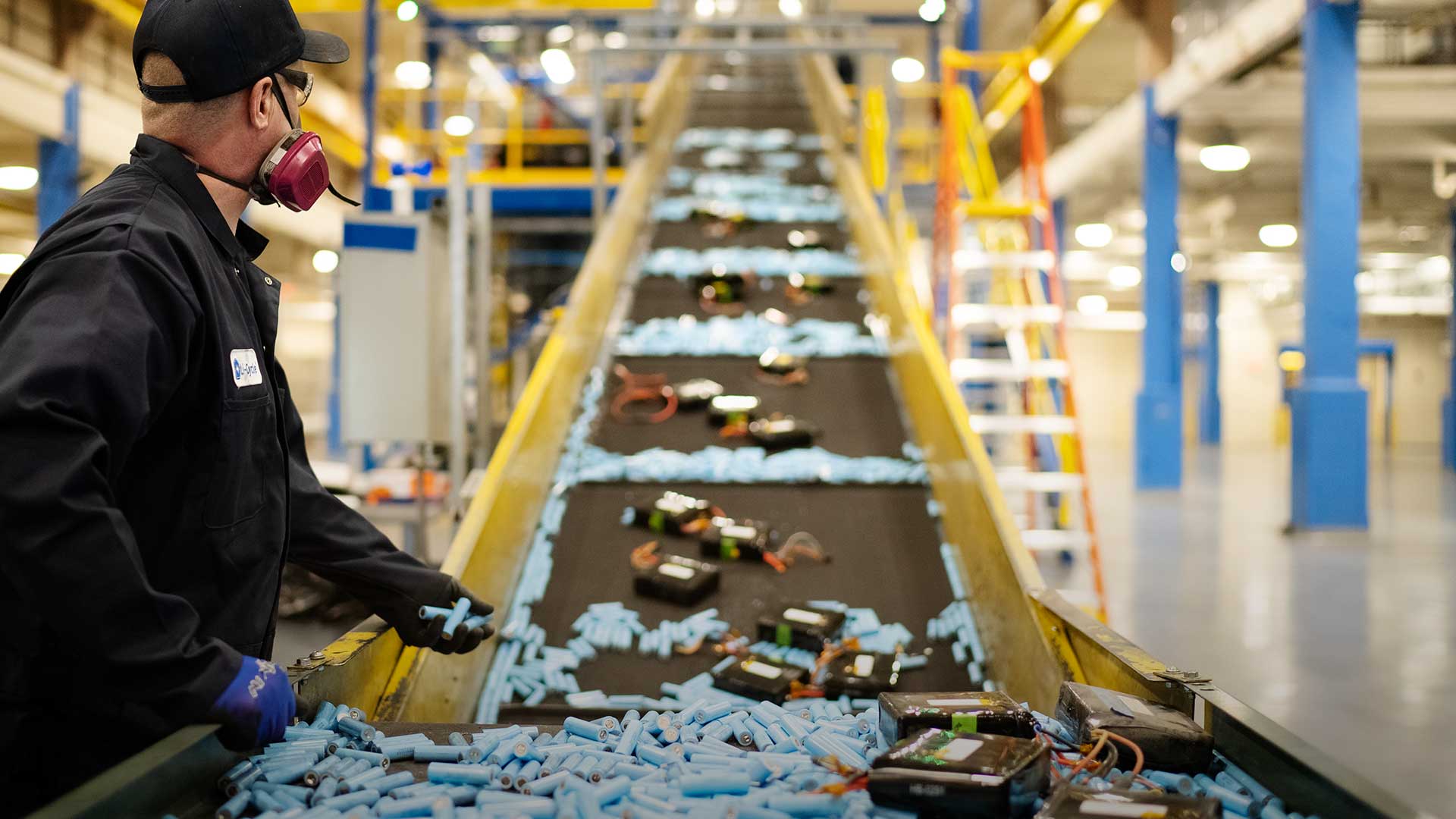
Electric vehicles have a waste problem. Canada has the solution
Innovative techniques for recycling batteries are closing the loop on EV emissions
Phasing out fossil fuel powered cars, trucks, and buses completely will eliminate around a fifth of current global emissions. Achieving net-zero goals relies, in large part, on electric vehicles (EV). But in the race to get EVs on the road, what happens to the battery when the vehicle reaches the end of its life? The answer lies in Canada’s burgeoning lithium-ion battery recycling sector.

Battery waste overload
“Lithium-ion batteries are a crucial part of decarbonizing our economy. But when they generate so much waste, it’s hard to see the advantage over fossil fuels,” says Tim Johnston, Executive Chairman and Co-Founder of battery recycling company Li-Cycle.
With a massive deployment of EVs expected in the next few years, the first wave of vehicles is expected to retire around 2027, producing vast quantities of battery waste.
“There are currently around 830,000 tonnes of lithium-ion waste globally. By 2030, that number will reach approximately 3.2 million tonnes,” says Johnston.
The lithium-ion batteries found in our laptops and smartphones are typically smelted down at present, with 40-50% of their materials recovered and sent into industries like steel production. It is a process that produces significant greenhouse gas (GHG) emissions. And because the recovered materials aren’t pure enough for batteries, new minerals must be mined for every device.
On top of that, emissions are generated in the globalized supply chains that typify the industry. “If you look at the battery supply chain today,” says Jean-Christophe Lambert, Business Development Manager at Lithion Recycling. “You’ve got all the minerals coming from South America, Africa, and Australia heading to Asia to be refined and put into batteries. And those batteries are either going to North America or Europe.”
Closing the loop
The solution is to cultivate EV supply chains that re-introduce battery materials from end-of-life vehicles, while minimizing carbon miles. For Canada, with its abundant mineral deposits and world-class automotive sector, companies like Li-Cycle and Lithion are the last step in closing the loop on such a localized, circular supply chain.
Both Li-Cycle and Lithion have their own patented solutions for recycling lithium-ion batteries, recovering approximately 95% of the battery’s materials, at a purity indistinguishable from freshly mined minerals. Lambert says this technology means that “batteries can be recycled indefinitely.”
The processes both have vanishingly low GHG emissions, especially when powered by renewable electricity, which Canada’s substantial hydroelectricity capacity can supply at low cost.
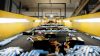
Both companies are focused on ensuring supply links are as short as possible. Lithion’s business model rests on forming localized hubs with cell manufacturers to minimize how far depleted batteries travel for recycling, as well as reducing the distance for recycled materials to find new life as fresh EV cells. Once its proof-of-concept operation in Quebec becomes a commercial plant in 2022, the company plans a rapid roll-out of 20 new facilities across North America and Europe.
Li-Cycle follows a similar model, using a rapid deployment modular system it hopes will enable the company to keep pace with ballooning demand as EVs become more commonplace. The company opened a new Spoke in Rochester, New York late last year, installing the facility in just four weeks of it being shipped from Li-Cycle’s factory in Ontario.
A Canadian solution
That these companies should emerge in Canada is no coincidence. As Johnston says, “There are very few countries with the natural resources to support the lithium-ion supply chain. It just makes sense that Canada should be a significant player in developing the circular EV supply chain.”
The presence of raw materials is already attracting fuel cell manufacturers keen to take advantage of short supply lines that could get even shorter once battery recycling scales. Stromvolt and Britishvolt have both recently announced they will be installing capacity in Canada, joining Ford and General Motors’ forthcoming EV assembly plants.
There are very few countries with the natural resources to support the lithium-ion supply chain. It just makes sense that Canada should be a significant player in developing the circular EV supply chain.
Tim Johnston, Executive Chairman and Co-Founder, Li-Cycle
The Canadian mining sector is also playing an instrumental role: Both Lithion’s and Li-Cycle’s chemical processes are borrowed in part from traditional refining methods. It’s an illustrative example of the cross-pollination that occurs when every part of an industry is in the same place, and indicative of Canada’s capacity to pioneer the future of EV production.
Canada isn’t the only country pursuing circular EV supply chains – and nor should it be. But with a clear abundance of skills and resources for every element of the EV ecosystem, Canada is building the template for low-carbon, low-waste production and creating opportunities for investment throughout the supply chain.
Read More
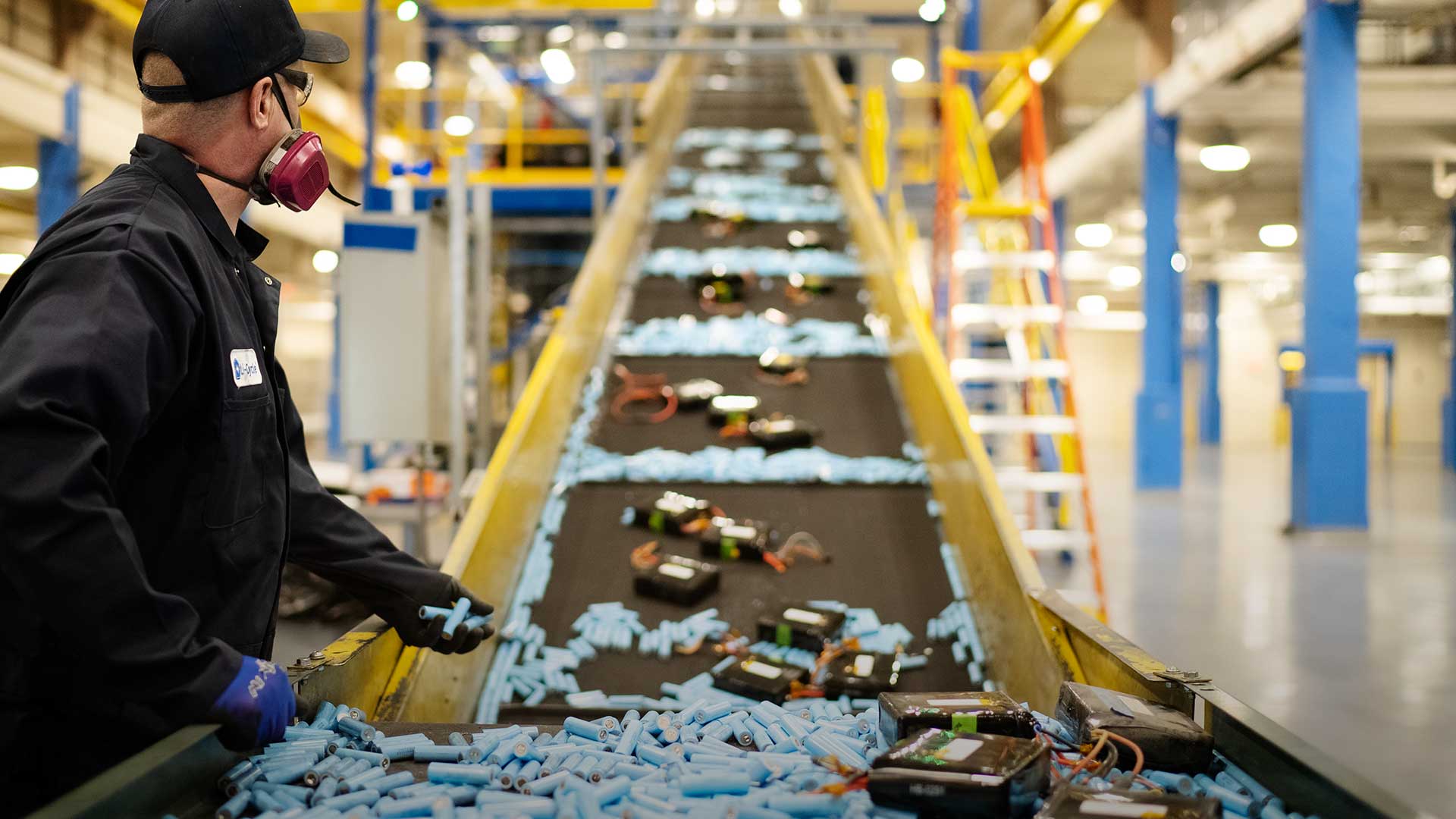